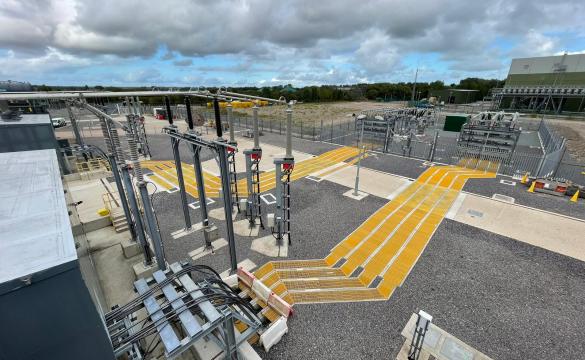
Substation configuration and build types
Each substation, whether existing or new, can have different configurations or equipment construction depending on what is needed, and to comply with regulations.
So what types of substation are there?
Some useful key terms and equipment definitions are included below:
Security and Quality of Supply Standard (SQSS): The SQSS is the minimum design standard used to plan transmission assets. It ensures safe and reliable operation across the transmission network. All new assets are compliant with these standards.
Substation bay: A set of equipment that connects a circuit into a substation. Bays can be connected to generation, such as renewable generators or demand, where high consumption of power requires direct connection, for example electrified railways. Each bay usually includes its own set of switchgear and transformer.
Switchgear: Includes a variety of equipment including disconnectors, fuses, and lightening arrestors often found in substations. This group of equipment ensures the safe disconnection of an electrical circuit when a fault occurs or can isolate a circuit when maintenance needs to be conducted.
Circuit breaker: Opens to break the circuit should a fault be detected, preventing the flow of electricity. A circuit breaker must be closed to resume normal operation of a circuit.
Busbar: A piece of metal that conducts electricity across its span. Equipment in substations is usually clamped directly on to these busbars.
Earthing: Equipment to direct the current to ground if a fault is detected, allowing excess electricity to escape. This helps to mitigate safety issues.
Transformer: Steps up the voltage of the electricity within the circuit, which in turn increases the current, so any efficiency losses over long distances can be mitigated. Transformers can also step down current from high voltage systems to distribute it locally.
Substation configurations
Depending on several factors, substations are often built to different equipment specifications. For example, the layout may be determined by the size or shape of the specific site, or by the type of connection that has driven the need for the site.
Single busbar
In this configuration, equipment is connected directly to the single busbar. Bays are laid out along this single stretch to provide an incoming and outgoing connection. These substations can work in smaller spaces and are very economical due to limited equipment. It is also relatively simple to operate and maintain in comparison to other configurations. However, because all equipment is directly connected to the single busbar, if a fault should occur or maintenance needs to be conducted, this would mean the disconnection or failure of all connected bays. Bays do however have individual breakers, meaning if a customer’s equipment should trip off, the rest of the circuit in the substation will not be affected. A single busbar substation would not provide a connection that is compliant with SQSS due to the lack of reserve power in case of fault or maintenance.
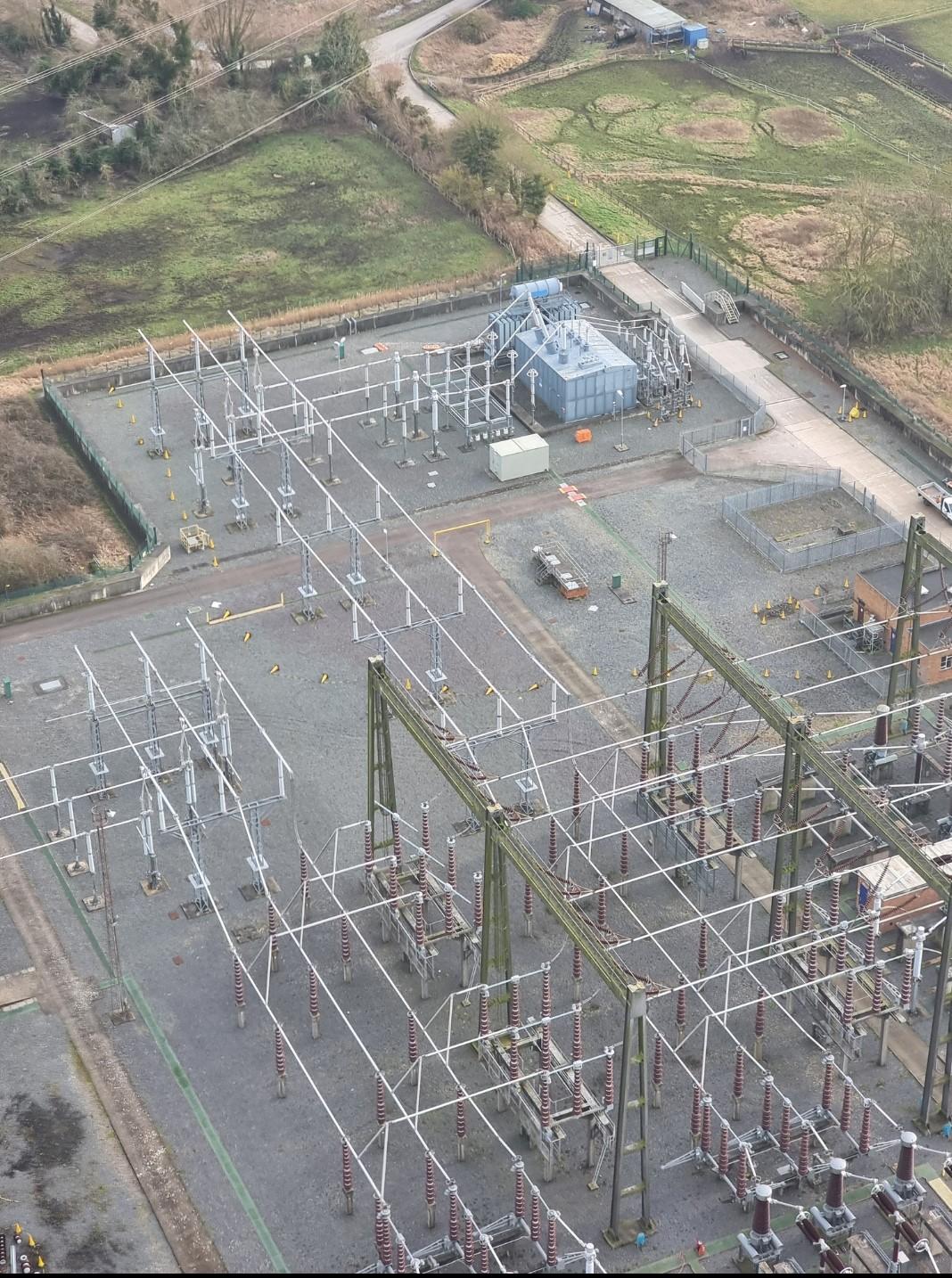
Double busbar
Equipment is all directly connected to a busbar and laid out in bays. However, with the double busbar configuration, a second circuit is present which can direct the flow of electricity onto a reserve busbar. This means there is greater flexibility in maintaining the equipment, as load from connected bays can be transferred over to the reserve busbar when needed. Equally, when a fault is detected, power can be switched to flow onto the reserve busbar, therefore preventing total failure. Again, like the single busbar- customers have individual breakers for safety and maintenance. This type of substation does occupy more space and requires more capital to build, making it unsuitable for certain sites. A double busbar substation typically provides an SQSS compliant connection, as it has a supply of reserve power in case of fault.
Mesh corner substations / compact mesh design substations
Mesh corner substations have a single busbar, which is arranged in a ‘square’ with four circuit breakers located to create isolatable corners. One corner can be taken out of service for maintenance, with the other corners remaining live. Owing to issues with the design behind a mesh corner arrangement, any fault generated on a feeder circuit into the substation, or on the generation connection itself would have the potential to trip all the equipment connected. This means they fall below the new minimum design standards for planning the transmission system, and customers connecting at these sites must have a non-firm or design variation as they are not compliant with SQSS. Mesh corner substations are typically found at 275kV on the Electricity Transmission System and were constructed under previous network design methodology, which differs from today. New mesh corner substations are not constructed due to these limitations.
Equally, most of these existing sites are in space constrained locations making extensions or modifications for connections extremely difficult.
Air Insulated Substations (AIS)
Rather than equipment configuration, this type of difference in substation relates to the insulation medium.
Air insulated substations use the physical air gap between equipment as the insulation. Generally built in large, open air spaces, careful consideration is given to the distance between busbars and other assets. As an example, the air gap required at 400kV is 3.1m. They are reasonably economic to build, as no costs are required to provide insulating gases, and there are usually minimal buildings constructed on site. The primary plant in an AIS substation, such as circuit breakers, can be electrically isolated and removed individually for trouble shooting if needed, as they are not built integrally into other pieces of equipment.
AIS sites do generally occupy a much larger physical footprint than gas insulated substations (GIS). Indoor double busbar AIS can also be built in areas of high pollutants, for example near to an industrial site or in salt air, which may mean it occupies an even larger footprint. Maintenance on AIS can also be resource consuming as all exposed components must be visually inspected , especially for copper corrosion caused by environmental exposure, and arcing can be more likely as not all parts are fully insulated. However, it is also easier to visually identify a fault on AIS, so issues can be clearly identified and resolved.
Gas Insulated Substations (GIS)
Gas insulated substations have historically used Sulphur Hexafluoride (SF6) gas as an insulating medium to provide insulation to the electrical equipment. Work is underway to phase out the use of SF6 for other alternative insulating gases - find out more here. These gases provide excellent insulating qualities with the result that the gap between electrical equipment can be vastly reduced. They are typically built indoors and occupy a smaller footprint than air insulated substations. This means they can be built in space constrained locations and are usually utilised in more built-up areas.
Insulated units can be monitored remotely via a variety of specific instrumentation, meaning less visual inspection may be required. However, as equipment is fully insulated, expert maintenance is required to isolate and de-pressurise parts of the system to identify faults and undertake works. They are more expensive to build due to the cost of gases, and the need to construct a containment building. The breakers used are also sealed for life, meaning if one fails, it needs to be completely replaced. New assets are also built with double busbar configurations to accommodate as many customers as possible, making them more economic and efficient to construct.
For more information on our new substation triggering and expansion processes, read our article here.