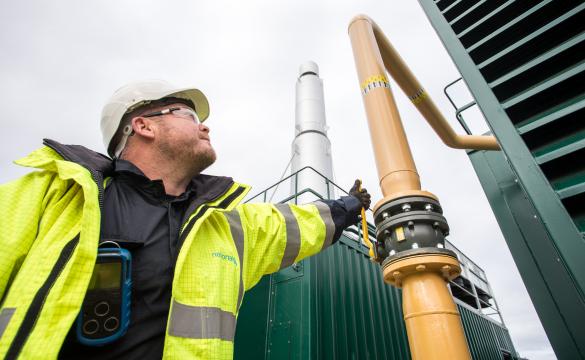
Staying safe, supporting vital services
How a pioneering safety culture has helped National Grid Metering respond to the challenges of the pandemic.
As the largest gas meter asset manager in the UK, National Grid Metering must uphold the highest safety standards. The imperative to safeguard the organisation’s people, partners and customers is integral to its operations, and has inspired an industry-leading safety culture. Most importantly, this distinctive approach has helped it act quickly and decisively in keeping the gas flowing for essential services during the Covid crisis.
Developed after detailed studies of many organisational culture models, the safety culture at National Grid Metering (NGM) is based on three principles: trust, report, learn. In practice, this means trusting the people who work directly with gas assets to report incidents, and then learning from this reporting to prevent similar incidents in the future. It’s a straightforward approach everyone in the organisation can understand immediately without special training – and this simplicity has been key to its success.
Perhaps more importantly, the safety culture works because it removes all blame. It recognises that, although around 80% of incidents involve some sort of human error, the root cause in most cases is a failure in systems, processes or practices. As Phillip Roberts, SHE Specialist at NGM, explains, “When things go wrong, it’s rarely the fault of the people concerned – there’s usually a more fundamental problem behind it. So when an incident is reported, any questions are not about ‘who’ is responsible, but about ‘how and why’ it happened.”
In this way, NGM learns from the incident much more quickly, and can get straight on with identifying and implementing the changes or improvements needed to avoid a recurrence. “We always look at the system or process first,” continues Phillip. “If we can make the system reinforce the desired behaviour, we can be sure we’re supporting our people in carrying out their work correctly and, above all, safely.”
No finger pointing means no delays
Crucially, because safety at NGM is all about learning rather than blaming, people feel comfortable in reporting incidents. They report them more readily and the organisation acts on them more quickly. And, as safety is so central to everything NGM does, this willingness to report incidents and learn from them speeds up the organisation’s operations and decision-making generally. This brings obvious benefits to all kinds of industrial and commercial customers, but has had a particular impact on those businesses that are essential to keeping the country running during the Covid pandemic. Where the repair or upgrade of gas-metering infrastructure has been vital to their continued operation, NGM has been there to carry out the necessary work swiftly.
In many cases, project lead times are being cut to less than a quarter of standard expectations. Even in complex situations, the need for essential services to maintain ‘business as usual’ has encouraged an agile approach among NGM’s leadership and engineers – an approach made possible by the organisation’s safety culture.
Above all, NGM has continued serving critical metering installations, with 53,000 planned site visits so far during the pandemic. The business has also continued to support gas supply consumers, reactively making over 80,000 site visits since the first lockdown. Throughout, its teams have maintained Covid-safe working practices, with dynamic risk assessments in place, and following World Health Organization guidelines as well as those of the Department for Business, Energy and Industrial Strategy.
Examples of NGM’s response to customers’ more pressing needs during Covid include its involvement with a major NHS hospital in the East Midlands. The team was working on a large remedial project on the primary IP metering installation, when another part of the hospital’s equipment – which was not NGM’s responsibility – failed unexpectedly. This caused a loss of gas to the vital steam boiler, and the NGM team on site could not leave knowing the hospital might eventually lose its hot water, heating and decontamination services. They assembled an extended team to help, and within two hours, the supply to the boiler was re-established and the hospital was back up and running safely.
In East Anglia, a provider of intravenous equipment to hospitals contacted NGM when a recently installed combined heat and power (CHP) system could not be commissioned correctly due to inadequate gas-supply pressure (the oversight of a designer involved in the system’s installation – again, not NGM’s responsibility). Understandably, the need for a pressure increase was extremely urgent. Technical Delivery Lead at NGM, Damian Murray, put together a plan to solve the problem as speedily as possible. In just a week, the team had installed all the necessary new equipment, completed the paperwork needed for the upgrade to take place, and brought the pressure up to the levels required for the CHP system to function effectively.
At a multinational pharmaceutical company’s manufacturing plant in the North-West, NGM planned to carry out remedial work on the gas infrastructure throughout 2020, as well as fulfilling an ongoing maintenance plan for the metering installation. This included examining two shell-and-tube heat exchangers, installed as part of the metering module, to ensure compliance with the Pressure Systems Safety Regulations 2000. As the Coronavirus pandemic developed during the first few months of the year, it became clear the customer would soon need to adapt and escalate operations at the site to contribute to the global response – specifically, to produce large quantities of vaccine. With this on the horizon, the NGM team accelerated its work there, and completed it by September, leaving the plant with a fully updated gas infrastructure, ready to meet the demands ahead. The early completion also meant NGM’s engineers were no longer on site, except for routine maintenance. As Technical Delivery Lead, David McRoy, said, “We could see the site was soon going to become extremely busy, so we pulled out all the stops to make sure we were out of the way at that critical time.”
As plastics have become increasingly important during the pandemic – for personal protective equipment, and many other medical uses – NGM’s work at a leading oil company’s ethylene plant in Scotland, took on a high degree of urgency during 2020. The customer is a critical link in the plastics supply chain, and proud of the fact that every person in the UK will touch something every day that contains raw material from this site. So there can be no interruptions to any of its operations, and this was particularly true during the last year. NGM has moved quickly to carry out all repairs and maintenance to the company’s metering installation – including a major painting programme during the summer months, ensuring vital outdoor equipment is fully protected against the harsh Scottish winter.
Preparing for the continuing impact of the pandemic, NGM is carrying out a complex metering upgrade at a Cheshire-based hospital, due for completion in the second quarter of 2021. The work will ensure the site has the gas capacity required to meet the ongoing challenges presented by Covid-19 – and, most importantly, that the installation provides the highest levels of reliability. Of course, timing will be critical, and the organisation’s safety culture will be central to meeting key deadlines.
Safety as a way of life
Maxine Long, who leads National Grids UK Metering business, sums up how safety is crucial to the organisation: “We strive continually to promote an open, transparent and positive culture, where we put the wholeness of everyone’s wellbeing at the heart of everything we do – and, of course, this includes their safety. The best way I can describe this is having a perpetual unease and constant desire that we can do things better for our people, our customers, our business and the communities we serve. Safety is deeply engrained within this and in our values as an organisation. Our leadership team has been successful in setting the tone: 97% of our people rate our safety leadership favourably, and we have seen year-on-year improvements. Customer feedback also shows how our safety culture is understood and appreciated externally.”
For Maxine, there’s always scope to do better: “We work to a drumbeat and momentum of continual improvement. We aim for absolute clarity of purpose and expectations, and this encourages ownership of safety reporting and decision-making. In short, our people have the freedom to help determine how work gets done, and that increases the pace of all our operations. By creating a virtuous circle of feedback, learning and trust, and investing in our people, we build capability and confidence – including the confidence to speak up to highlight concerns over safety or otherwise.”
NGM’s commitment to its safety culture is translating into some impressive figures. As Maxine says, “This year, we have seen record levels of customer satisfaction, at 87%, and the confidence that we’ll take action on feedback is at 92%.”
It’s very clear NGM takes its safety responsibilities seriously. The organisation’s leadership and engineers are much more than experts in gas metering infrastructure. They are also participants in an exemplary organisational culture, built on blame-free openness, widespread employee engagement, and a potentially life-saving clarity of communication.